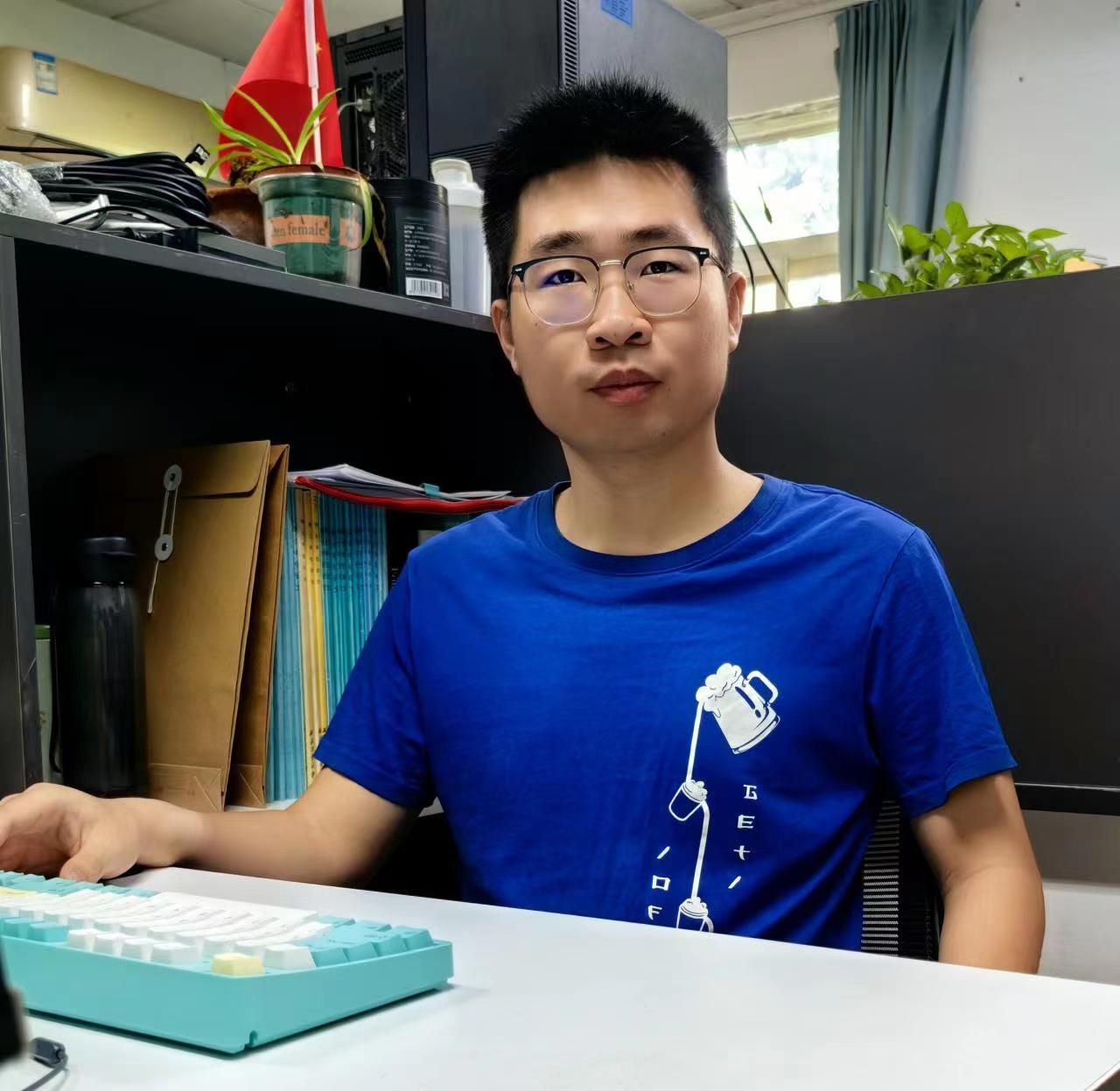
标题:考虑强度的连续碳纤维增强3D打印路径规划方法
英文标题:Field-based path planning method for continuous carbon fiber reinforced 3D printing
作者:窦浩
指导教师:张定华 教授
培养院系:机电学院
学科:航空宇航制造工程
读博寄语:长风破浪会有时
主要研究内容
立足于连续碳纤维增强 3D 打印技术体系,以现有的切片工艺为基础,研究工艺过程中的基于强度的打印路径规划,避免打印过程中的跳点,重叠等,进一步发挥碳纤维在结构中的增强作用,并且充分考虑到打印件在实际工况中的使用情况,根据零件的载荷分布进行合理的铺放排列纤维,最大化结构的承载能力;在此基础上通过连续碳纤维增强3D打印试件的力学性能仿真,对设计的打印件建立力学性能有限元仿真模型,对打印制件展开多尺度力学结构研究;连续碳纤维增强3D打印中碳纤维与基体材料的相互渗透并浸渍结合,通过建立基于工艺参数的原位浸渍的浸渍程度评估方法,将力学性能与打印参数结合,对试件的浸渍程度进行评估,以优化3D打印工艺参数。
基于此,本项目依托航空发动机高性能制造工业和信息化部重点实验室、航空发动机先进制造技术教育部工程研究中心,在西北工业大学博士论文创新基金的资助下,针对上述内容展开研究。本项目属于重要研究前沿,在中国工程院《全球工程前沿2020》机械与运载工程领域,“连续纤维增强复合材料增材制造”位列工程研究前沿第五位,具有极其重要的理论研究及实际应用价值。主要完成的研究内容如下:
一、基于强度的连续碳纤维增强 3D 打印路径规划
完成 3D 打印基体材料在打印过程中的材料相关性的相关研究,通过标准压缩实验阐明了不同材料在同种工艺参数下的打印件的力学性能;完成基于模型的切片以及路径生成算法研究。针对连续碳纤维3D打印路径规划,实现复杂结构路径的连续性,完成了模型切片处理和单层切片内的路径生成;实现基于外载荷的连续碳纤维增强3D打印路径规划。针对工程中经常出现的零部件,分别采用标准件,方型连接件,吊钩承重件三种典型应用场景下的制件,基于FFF增材制造成型方式,分别使用“Zigzag”、“平行轮廓”和“基于强度”的打印路径完成制件的打印。并按照力学性能仿真—拓扑优化—优化结构—力学性能仿真—…—优化结构的优化方案,分别得到多组不同几何信息的结构,继续打印完成对应的制件,进一步分析“纤维路径”与“几何结构”相结合的连续碳纤维对3D打印复合材料的增强效果。
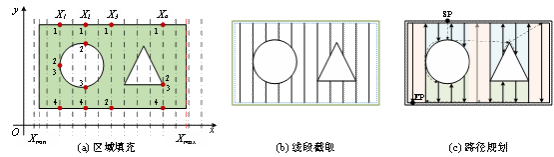
图1-1 打印区域路径规划过程
二、连续碳纤维增强3D打印制件的力学性能有限元仿真方法
结合连续碳纤维与聚乳酸的材料属性参数,建立了连续碳纤维增强3D打印复合材料的直接参数化仿真模型。使用的材料分别为增强相HTA 40 1K连续碳纤维,基体材料FlashForge 1.75mm 聚乳酸线材,使用商业仿真软件ABAQUS结合连续碳纤维和聚乳酸的基础力学性能参数对结构直接进行力学性能仿真,连续碳纤维与聚乳酸的结合方式采用共节点连接和嵌入式连接两种方法,根据模型尺寸和连接方式分别划分网格。分别采用不同的连接方式对连续碳纤维增强3D打印复合材料蜂窝结构进行直接参数化仿真。
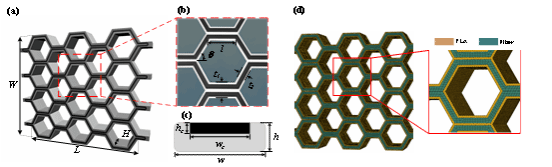
图2-1 仿真示意图
由于3D打印连续碳纤维增强复合材料为三维各项异性材料(正交各向异性材料),故根据广义胡克定律对其进行应力应变分析建立材料的本构方程,设计打印制件并进行力学测试以求取方程系数,得到本构方程以预测制件的宏观力学性能。
连续碳纤维增强3D打印制件在微观层面上的非连续性、各向异性以及各相的相互作用表现出复杂的宏观和细观特征,但是具有简化分析的可行性,即具有一定的结构均匀性特征。由此可以定义代表整个结构平均值的代表体元(RVE),RVE的概念类似于晶体的单胞,是材料或者结构的周期性组成单元。基于RVE建立的细观力学模型,可以在没有显著精度损失的条件下对结构的力学性能简化分析。细观力学模型可以将非均匀细观结构转换为局部的细观力学模型和全局分析,在这个过程中需要在单胞层面上分析结构细观力学性能,得到材料的平均有效属性,继而进行宏观的力学性能分析,有效属性的建立过程如图:
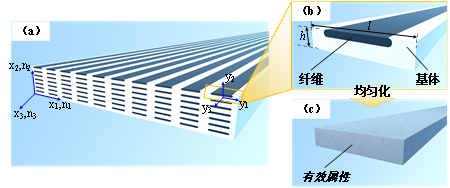
图2-2 连续碳纤维增强复合材料结构均匀化分析有效属性
用碳纤维体积分数为16%,相对密度为40%的3D打印CCFR蜂窝结构进行落锤低速冲击实验研究,并设置对比实验(无增强蜂窝,蜂窝相对密度一致)对比分析实验结果。实验结果分析如图2-3,在预定义的失效条件下,两种不同材料结构的冲击力分别为512N和1353N(2.64倍),比吸能分别为173 J﹒Kg-1 和537 J﹒Kg-1(3.10倍)。

图2-3 (a)纯PLA蜂窝低速冲击实验结果,(b)3D打印CCFR蜂窝低速冲击实验结果,(c)纯PLA和CCFR蜂窝冲击实验结果对比
为了更好地评估结构的抗冲击性,采用工业锥束CT无损检测技术对蜂窝结构的内部冲击损伤进行检测,冲击后结构出现明显的内部分层现象,根据CT扫描图像层数,分层部分出现在结构的上部,即冲击会改变试样的层间状态,从而导致打印层之间的分离和纤维-基体界面的失效。裂纹平行于纤维方向并在所有切片中扩展,导致裂纹穿透整个制件。可以得出结论,相邻打印路径之间的粘合强度是限制结构力学性能的重要因素,也是基体纤维浸渍性差的表现。
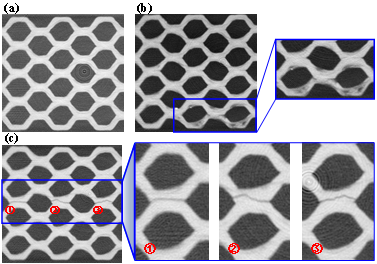
图2-4 CT检测结果:(a)试件实验前,(b)冲击导致的分层,(c)基体材料裂纹
三、基于工艺参数的原位浸渍的浸渍程度评估方法
对于连续碳纤维增强3D打印复合材料,施加在基体材料上的外力通过结合界面传递至连续碳纤维上,这也是CCFR结构强度得以增加的主要原因。然而,由实验分析得知CCFR 3D打印制件的纤维-基体的结合程度并不理想,界面处存在较大的孔隙,制件在外载荷下的主要失效情况是结合界面的破坏,致使纤维被从基体材料中拔出。为了更好的剖析纤维-基体的结合机理,使用锥束CT和扫描电镜对制件的损伤形态进行微观形态的分析,下图3-1为在压缩载荷下CCFR蜂窝的检测结果,在受到外载荷时结构未发生损伤,但有多个纤维被拉出。用场发射扫描电镜观察发现,连续碳纤维暴露在基体材料的外侧,主要原因是连续碳纤维在打印过程中主要靠牵引力铺设,因此,它的一部分附着在基体材料的表面,而不是完全被包裹,导致只有少数纤维而不是整个纤维束被基体浸渍,致使纤维-基体界面强度不足,在承受较大载荷时容易破坏,导致纤维-基体分离。为了通过增强纤维-基体结合界面来提高打印完成制件的力学性能,现已设计超声振动辅助浸渍法来提高制件的纤维-基体界面强度。
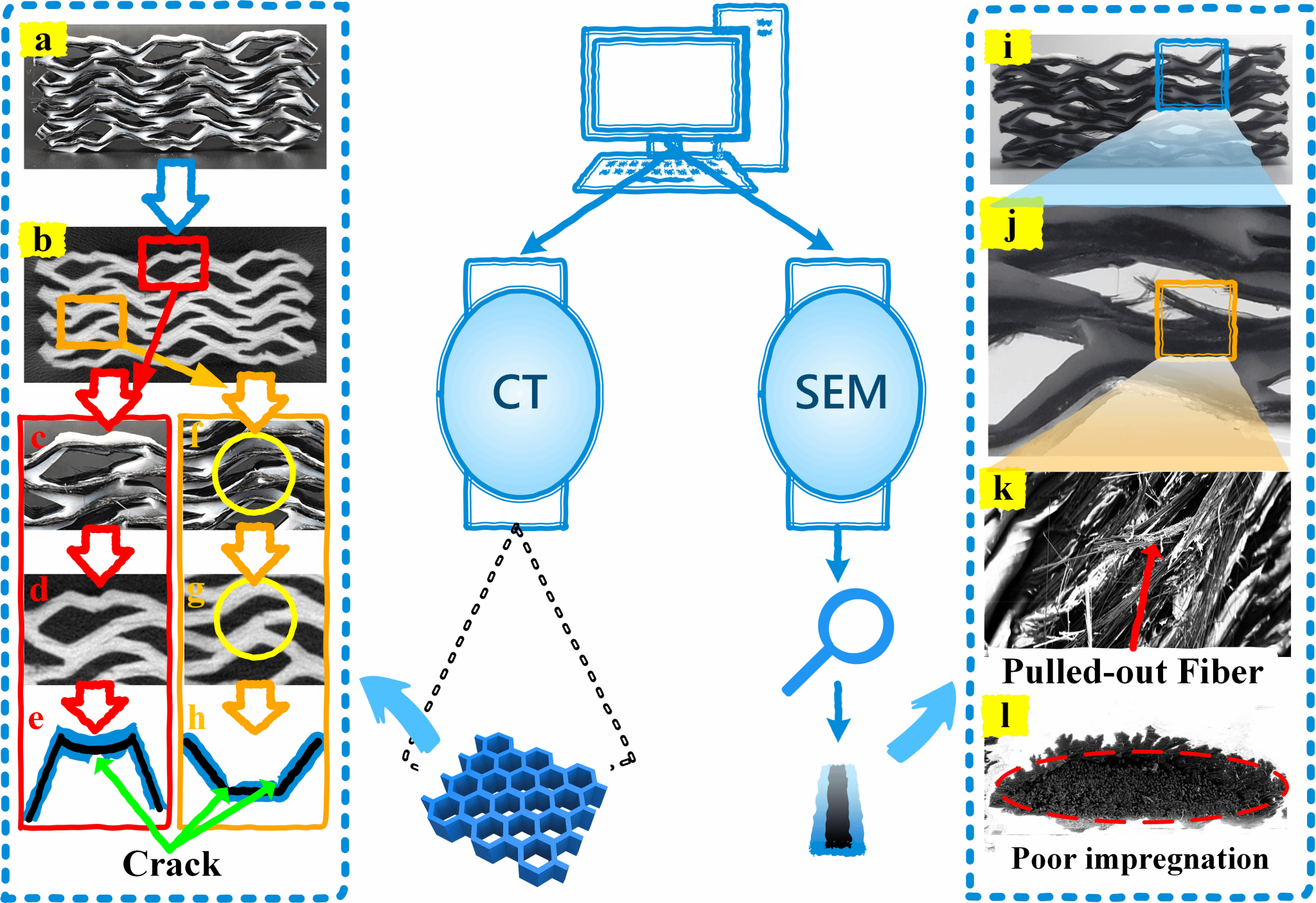
图3-1检测结果,(a-b)CT检测,(c-e)水平壁损伤,(f-h)倾斜壁损伤,(i-k)损伤区域SEM图像,(l)打印截面SEM图像
主要创新点
1) 基于强度的CCFR 3D打印路径规划方法。提出的CCFR 3D打印路径规划可以根据打印件的实际工况条件,结合碳纤维的力学特性,科学地规划打印路径,弥补碳纤维增强作用发挥不足的缺陷。
2) CCFR 3D打印制件的力学性能仿真方法。提出针对CCFR 3D打印制件的力学性能有限元仿真方法,建立细观力学模型和宏观力学本构模型,以解决连续碳纤维增强3D打印制件无法仿真的问题并提高仿真精度。
3) CCFR 3D打印制件纤维-基体材料结合机理研究。以锥束CT&SEM微观图像和宏观力学性能结果为基础表征纤维与基体材料的结合状态,据此建立纤维-基体材料浸渍机制以反馈优化打印工艺与仿真研究。
代表性创新成果
[1] H. Dou, Y. Cheng*, W. Ye, D. Zhang, J. Li, Z. Miao, S. Rudykh*, Effect of Process Parameters on Tensile Mechanical Properties of 3D Printing Continuous Carbon Fiber-Reinforced PLA Composites, Materials (Basel). 13 (2020) 3850.
[2] H. Dou, W. Ye, D. Zhang, Y. Cheng*, Y. Tian, Compression Performance with Different Build Orientation of Fused Filament Fabrication Polylactic Acid, Acrylonitrile Butadiene Styrene, and Polyether Ether Ketone, J. Mater. Eng. Perform. 31 (2022) 1925–1933.
[3] H. Dou, W. Ye, D. Zhang, Y. Cheng*, K. Huang, F. Yang, S. Rudykh, Research on drop-weight impact of continuous carbon fiber reinforced 3D printed honeycomb structure, Mater. Today Commun. 29 (2021) 102869.
[4] H. Dou, W. Ye, D. Zhang, Y. Cheng*, C. Wu, Comparative study on in-plane compression properties of 3D printed continuous carbon fiber reinforced composite honeycomb and aluminum alloy honeycomb, Thin-Walled Struct. 176 (2022) 109335.
[5] H. Dou, W. Ye, D. Zhang, C. Wu, K. Huang, T. Sun, Y. Cheng*, Three‐Point Bending Properties of 3D‐Printed Continuous Carbon Fiber Reinforced Heterogeneous Composites Based on Fiber Content Gradients, Adv. Eng. Mater. 2200829 (2022) 2200829.